Le Voyageur, un savoir-faire unique
Mer. 7 Septembre 2011 5756 vues
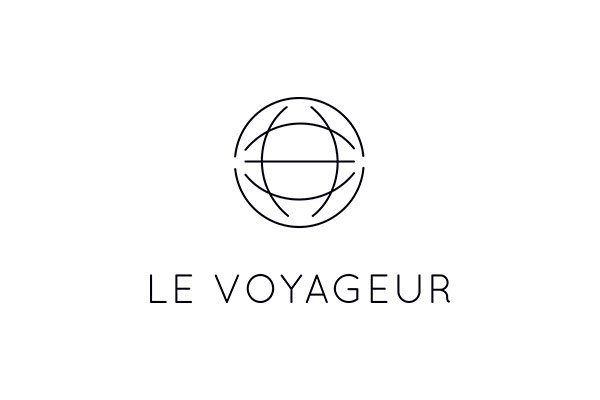
Entité à part entière du groupe Pilote, Le Voyageur dispose de son unité de production propre sur le site de La Membrolle-sur-Longuenée. Sur une surface de 30.000m2 de terrains dont 6.000m2 sont dédiés à la construction sur-mesure des camping-cars Le Voyageur, le constructeur y produit ici ce qui fait l’essence de sa réputation et de son savoir-faire. 80 personnes travaillent sur cette usine.
Tous les camping-cars Le Voyageur sont fabriqués avec une carrosserie toute en polyester et ossature duralinox . C’est une des spécialités du constructeur qui met en avant sa totale maîtrise du process de fabrication à partir d’un concept monobloc.
Les ouvriers préparent la carrosserie toute en polyester en partant du bloc du toit avec un système de moule. Les moules sont en préparation. Il faut compter entre 50 à 55 moules pour réaliser la totalité d’un véhicule. Pour y parvenir, Le Voyageur utilise différentes couches de résine. La première étape consiste à laminer les différentes couches afin d’éviter que des bulles se forment entre les couches. Cela demande une main d’oeuvre importante sur ce poste de production où les « robots » ne sont pas présents.
Les moules sont au préalable achetés et ensuite développés dans l’unité de production du constructeur à La Membrolle-sur-Longuenée. Tout le travail de préparation est manuel et se base sur la même conception que celle d’un bateau.
Nous assistons ici à la projection de fibre sur le moule. Les ouvriers placent du « gel coat » dessus. En durcissant, le « gel coat » fixe la fibre, une fois sèche, on peut retirer la pièce du moule afin de l’envoyer en fabrication.
Les pièces terminées, comme ici avec le toit d’un intégral, sortent de l’atelier polyester. Le toit de la gamme LVX est fait sur un seul moule, confirmant la réputation du Voyageur de produire des toits monoblocs et à recouvrement tout polyester. A noter que sur les RX Platinum, seuls les tiroirs bas de caisse ne sont pas en polyester mais en aluminium.
Il faut compter une journée entière pour fabriquer une pièce. Le Voyageur se base sur un critère de base «simple » : Un véhicule par jour, une pièce par jour. Chaque véhicule produit est un camping-car déjà commandé.
La phase de démoulage, une action très précise réalisée avec soin. Chaque pièce porte le nom du client et du véhicule commandé. Une fois la commande passée, il faut compter environ six mois pour recevoir son Voyageur.
Depuis l’arrivée de la seconde gamme (RX Platinum), deux process de fabrication des parois existent. On reconnait ici les parois d’un Platinum qui se différencient de celles du LVX par leur aspect « droit » sans « cassure ».
L’isolation du RX Platinum est plus épaisse que celle du LVX. Au niveau du plancher, elle est de 78mm et 48mm en ce qui concerne le panneau.
Nous entrons désormais dans le poste de préparation du châssis. Le Voyageur ne travaille qu’avec le porteur Mercedes avec, cette année, l’exclusivité du 6 tonnes en double-essieu arrière (une exclusivité renouvelée pour l’année à venir).
Le client vient à l’usine pour établir le plan de son véhicule, en fonction des nombreuses possibilités qu’offre Le Voyageur. C’est une façon de customiser à sa guise son camping-car. Une fois les plans établis, il repart avec le plan en question pendant que le constructeur se lance dans la production du véhicule. Le client peut, s’il en a envie, revenir voir l’évolution de la production de son camping-car.
Le châssis entre sur la chaîne de travail avec en parallèle le travail du plancher (et du mobilier pour les étapes suivantes). A noter que dans cette unité de production, une menuiserie intégrée existe et facilite le travail des ouvriers.
Le processus de fabrication d’un intégral Le Voyageur est particulier, car il s’effectue avec la pose d’abord de la paroi et ensuite celle du mobilier. Ceci a comme avantage que tout le mobilier passe par la porte cellule, donc, tout ce qui est à changer éventuellement ensuite peut sortir par la porte sans démonter la paroi.
Les parois sont donc posées sur le châssis nu (juste orné du plancher). On note que les circuits du chauffage ALDE sont placés contre la paroi et sous le double-plancher. La menuiserie est intégrée à l’unité de production. Ce qui donne un énorme gain de temps et de productivité. On y trouve les trois boiseries différentes qu’on peut trouver dans un Le Voyageur (Poirier, Teck, India). Le mobilier est fabriqué dans la menuiserie. Une fois montés, les meubles sont mis dans un chariot et amenés sur la chaîne de production. Nous assistons à l’étape de montage de la face avant ainsi que des ouvrants. Les meubles ne sont pas encore installés à l’intérieur du camping-car. Cette étape consiste également à s’occuper des pré-câblages, des bas-de-caisses et des tiroirs des bas-de-caisses. La carrosserie est terminée sur cette étape également.
Le mobilier de l’intégral est prêt à être installé. Tous les meubles passent bel et bien par la porte d’entrée sans exception, y compris le lit « intégral ». Tout est pensé pour être modulable et interchangeable. Le montage des meubles est le poste le plus long en termes de temps de travail. Sur cette étape, on se rend compte de la personnalisation de chaque véhicule.
En série, chaque véhicule est équipé d’une batterie cellule de 200 ampères, d’un panneau solaire de 100W.
Le montage du mobilier se poursuit avec notamment un gros travail sur la pose des lits arrière et intégraux. Les sommiers à lattes sont installés ainsi que les mécanismes pour les actionner. A ce stade de la fabrication, les ouvriers posent la nouvelle porte Hartal sécurisé en trois points. Le travail de la domotique s’effectue également sur cette étape (ici sur le Platinum). Sur les intégraux Le Voyageur, vous avez également la possibilité de ne pas avoir de porte chauffeur comme sur ce Platinum. Ceci offre une meilleure isolation au véhicule mais également une meilleure rétro vision au niveau de l’angle de vue du rétroviseur. Sans la porte chauffeur, vous avez également un rangement en plus. La chaine de production arrive à sa fin. Les dernières finitions sont effectuées à l’intérieur de l’intégral. Le mobilier est définitivement fixé, on ajoute les nouvelles finitions de poignées de portes des tiroirs et placards. Tout au long de la chaine, différents contrôles de qualité sont faits par les ouvriers. En fin de chaîne, les derniers contrôles s’effectuent. Ici, on contrôle le gaz, la mise en marche de tout l’électro-ménager, notamment le réfrigérateur. On procède également au nettoyage intérieur avant de le faire sortir pour le nettoyage extérieur, dernière action avant de le livrer à son propriétaire par porteur.
L’intégral Le Voyageur est fini, nettoyé, testé et contrôlé. Il est apte au service.